Technologia druku 3D
Podczas badanego w ramach grantu procesu produkcyjnego postanowiliśmy przedstawić produkty wytwarzane w ramach procesu w świecie rzeczywistym, jak i wirtualnym. Wizualizację produktów w świecie cyfrowym zrealizowaliśmy za pomocą technologii AR. Zapraszamy do zakładki Technologia AR.
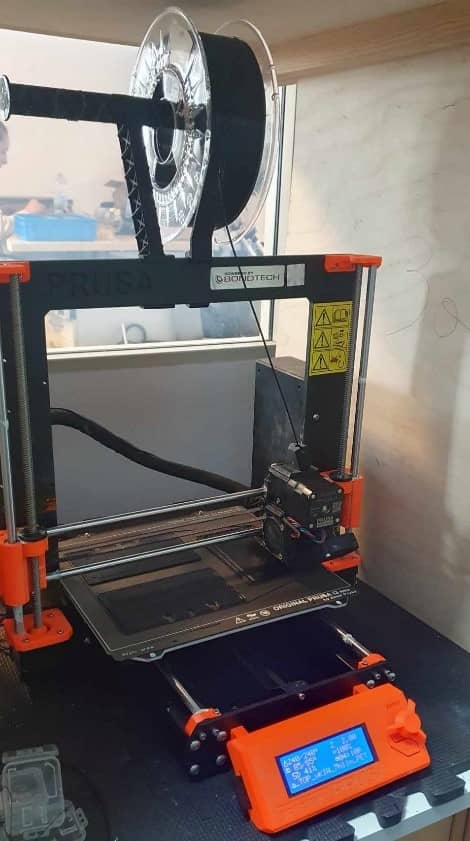
Przedsiębiorstwo wytwarza zaworu na potrzeby realizacji zamówień od klientów. Zawory są wykonywane z odpowiedniego materiału. Wizualizację wyrobu w świecie rzeczywistym można również przedstawić z wykorzystaniem technologii druku 3D. Druk 3D, tak jak w przypadku zwyczajnego druku, jest bardzo szerokim narzędziem oferującym nam przeróżne metody tworzenia form trójwymiarowych. Z uwagi na prostotę w obsłudze i łatwe w zrozumieniu oprogramowanie zdecydowaliśmy się na druk FFF, czyli Fused Filament Fabrication. W tej technologii drukarka rozgrzewa filament, czyli nasz materiał do wykonania zaworu, do odpowiedniej temperatury, a następnie za pomocą dyszy układa materiał na płytce produkcyjnej warstwa po warstwie zgodnie z ustalonym schematem.
Właśnie dlatego zanim zastosowaliśmy druk 3D, musieliśmy przygotować modele zaworu w taki sposób, aby po cały procesie drukowania zostały nam całe zawory, a nie góra filamentu.
Pierwszym krokiem było zbudowanie modelu zaworu. Szczęśliwie modele cyfrowe wyrobów uzyskaliśmy od producenta, czyli firmy Danfoss. Jednakże opracowane modele nie mogły zostać wykorzystane do zaprogramowania wydruku 3D. Powodem tego było złe rozszerzenie plików oraz niedokładności związane z rozmieszczeniem i wielkością otworów czy śrub. W celu przygotowania modeli do druku, używaliśmy dwóch programów, Solidworks oraz PrusaSlicer.
W programie Solidworks dokonaliśmy dostosowania zbudowanych modeli cyfrowych do wymagań stawianych przez zastosowaną technologię druku 3D. Więcej o budowie modelu w zakładce „Model 3D wyrobu”.
Następnie przygotowaliśmy opracowane modele do druku 3D. Wiązało się to najpierw ze zmianą rozszerzenia pliku, co dzięki użyciu prostych konwerterów (dostępnych w wersji online)nie sprawiało problemów i zostało przeprowadzone sprawnie.
Pliki wgraliśmy do oprogramowania PrusaSlicer. Jest to program pozwalający przygotować model 3D bezpośrednio do wykonania wydruku. Program ten umożliwia również opracowanie podglądu modelu na płytce do drukowania i uzyskania odpowiedzi na najważniejsze pytanie, czy zmieści się w obrębie wydruku. Co ważne, wspomniany program PrusaSlicer jest darmowy, ponieważ powstał jednocześnie z całym projektem drukarek Prusa, współfinansowany przez Unię Europejską. Zdaniem wielu ekspertów program ten jest najbardziej użyteczny w przypadku używania drukarek Prusa. Należy również wspomnieć, że większość nowoczesnych drukarek jest kompatybilna z tym oprogramowaniem. W naszym przypadku, wykorzystania drukarki Prusa, model i3 MK3S, kompatybilność nie stanowiła dla nas problemu.
Rysunek 2. Zbliżenie na model topu w programie PrusaSlicer pokazujące niedokładność zaokrągleń w modelu
Po wgraniu modeli do Slicera niestety ponownie okazało się, że dokładność elementów okrągłych nie jest na wystarczająco dobrym poziomie, aby uzyskać gładki wydruk. Problem ten wynika z algorytmu prowadzącego do ułatwienia procesu druku oraz skrócenia czasu jego trwania. Na szczęście zastosowane rozwiązanie nie było trudne. W ustawieniach programu określiliśmy szczegółowość modelu zgodną z wartością modelu, który wgraliśmy do Slicera co rozwiązało problem.
Wcześniej wspominaliśmy, że program pozwala zwizualizować podgląd modelu na danej drukarce. Okazało się to dla nas bardzo istotne, ponieważ jeden z modeli (korpus), nie mieścił się w obszarze roboczym. Oznacza to, że w przypadku wykonania wydruku część modelu zostałaby obcięta, nie zostałaby wykonana. Dzięki wykonanej wizualizacji uniknęliśmy niepotrzebnego problemu (nieprawidłowego druku – skutkującego zużyciem materiału i niepotrzebną eksploatacją maszyny) i zmniejszyliśmy skalę wszystkich modeli do 90% oryginału.
Zmiana rozmiaru innych pozostałych modeli była podyktowana chęcią złożenia całego zaworu w całość, czyli wszystkie elementy muszą być wykonane w tej samej skali. Gdybyśmy zmniejszyli tylko korpus, części nie pasowałyby do siebie.
W tym momencie duża część pracy została już zakończona, jednakże cały proces się nie skończył. Pozostało nam jeszcze wydrukowanie testowych modeli półproduktów i wyrobów, a następnie wydrukowanie finalnych kopii wszystkich elementów. W tym celu musieliśmy wykonać jeszcze jeden krok w Slicerze – mianowicie dodania do zbudowanego modelu elementów odpowiednich wypełnień i podpór. W przypadku druku warstwowego modeli mających puste przestrzenie czy otwory wymagane jest wypełnienie tej przestrzenie specjalnie zaprojektowanymi podporami. Podpory te zbudowane są z tego samego filamentu, z którego wykonany jest wydruk, jednakże są one nałożone w większych odstępach celu późniejszego łatwiejszego usunięcia z modelu. Wspomniane podpory okazują się niezbędne – bez nich cały wydruk załamałby się pod swoim ciężarem, natomiast filament ściekałby po ściankach na dół (z uwagi na siłę grawitacji) zamiast układać kolejne poziomy wydruku.
Dzięki przedstawionym i opisanym krokom i działaniom byliśmy w stanie przejść do druku finalnych kopii. Zawory wydrukowaliśmy w trzech kolorach. Jedną kopię w kolorze naturalnym, natomiast pozostałe części w kolorze czarnym i pomarańczowym. Kopia w kolorze naturalnym zostanie złożona i będzie przedstawiać pełny zawór, gdzie pozostałe części są dostępne do samodzielnego złożenia. Natomiast wydruki wykonane w kolorze kontrastującym mają na celu rozróżnienie granic poszczególnych .